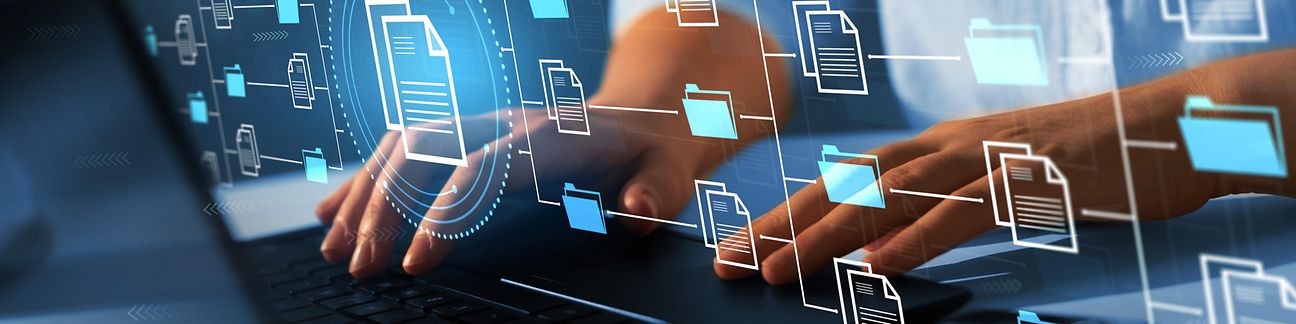
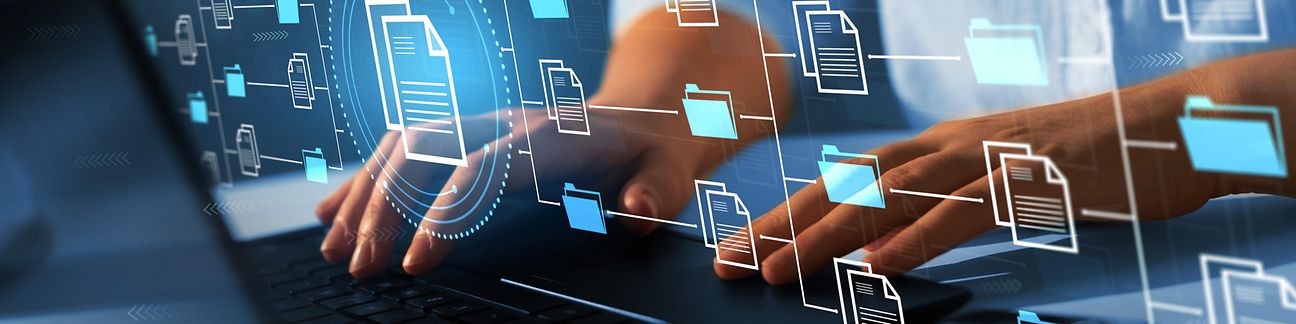
Factory of the future
The German Mechanical Engineering Industry Association (VDMA) sees two major challenges for the near future: the lack of planning security due to political and economic risks, and the restructuring of the automotive industry.
New orders at German mechanical engineering firms already declined in 2019 – and it doesn't look like things will improve in 2020. Digitalization is a potential answer, but entails capital expenditures in times of declining revenue. Companies are currently only prepared to invest if the investments have a swift impact.
Three areas seem particularly promising here: the development of new products and services, closer integration with customers and partners, and productivity improvements. Three examples:
Novel services – the value of data
More and more machines are getting connected and learning to communicate. They deliver a constant stream of data, from which valuable information can be obtained. Companies can sell this data in addition to their own products.
Closely integrated value chains – transparent, fast, and efficient
Digitalization moves suppliers, manufacturers, and customers closer together. This, in turn, makes processes transparent and faster, and thus more efficient.
Human-machine interface – avoid mistakes, optimize processes
Augmented reality and geodata services help low-skilled workers to avoid mistakes and save time. Virtual reality supports knowledge transfer. And user interfaces are especially helpful when they adapt to their respective environments. Digitalization makes all of this possible.
How can it work? Capturing the value of data involves two steps
The first step is an intellectual one. It involves a change of perspective: data processing must be perceived as an integrated whole. All too often, information technology, operating technology, and development technology work in separate data worlds. These silos have to be broken down. Digital twins, for example, assist in making the right strategic decisions. The development department turns these new decisions into a new product. And ultimately, the production department builds that product. Connecting these areas with one another speeds up the innovation cycle.
The second step is technical: the new 5G (fifth generation) mobile communications standard can connect up to a million devices per square meter faster and more reliably. It transfers more data per second. And it enables localization precisely to ten centimeters. 5G is an enabler for manufacturing companies that want to take advantage of the benefits of technologies like machine learning, augmented reality, Internet of Things, and cloud computing.
Find out more about the factory of the future and digitalization as an answer to a lack of planning security and restructuring in our white paper.